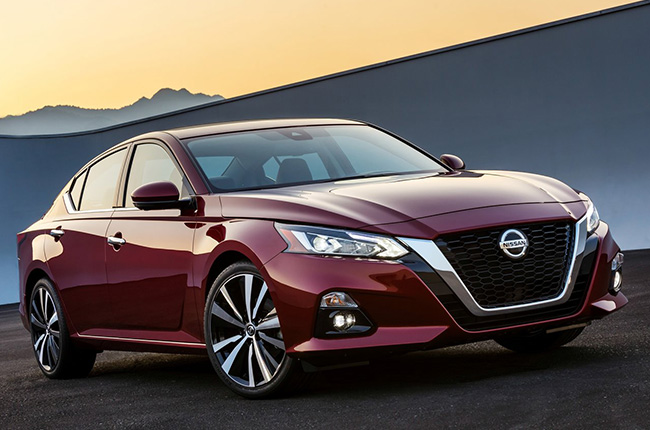
The Nissan Altima’s engine gets the same treatment as the GT-R. With high-end manufacturing techniques getting more refined, Nissan feels it is high time to let one of its processes trickle down to some of its more complacent models.
As we all know, an engine sits at the heart of the driving experience. Without it, a car is just a fancily sculpted box with wheels. As such, an engine should be heavily invested in by automakers since consumers demand performance, reliability, and fuel efficiency from these machines, day in and day out.
The Nissan GT-R was the first to sport the state-of-the-art Mirror Bore process. The process that was once reserved for small volume manufacturing is now available for mass market vehicles. Nissan is capable of churning out 1.4 million engines per year, or one every 19 seconds at the Decherd Assembly line and the brand has recently applied its technology to the production line. This is a first for the price point and volume that the Altima commands.
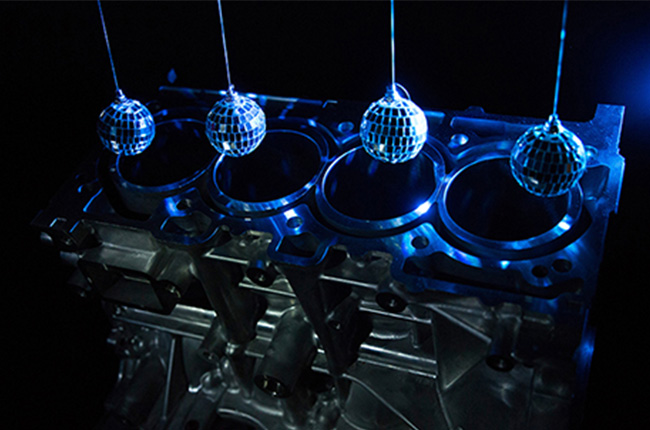
The Mirror Bore process involves charged metal wire being blown as gas is used to atomize the material in order to coat the cylinder walls of the engine. The thickness of the coating comes in at only 200 microns thick, or 2mm. This is about twice the thickness of an average human hair or about three times thicker than your average grain of salt.
The second stage involves diamond polishing that gives the coating a mirror finish that is as smooth as possible to ensure that the piston moves efficiently in the cylinder wall. The Mirror Bore process results in a – you guessed it – mirror-like finish inside the cavity for the piston. A specialized drill bit is used in order to ensure the smoothness of the finish. A cylindrical tool with diamonds adorning its perimeter cut and polish and give the engine the performance that it needs.
For years, manufacturers and oil companies have been working hand-in-glove to develop engine lubricants that reduce friction so that the engine may be able to move easier, but what if the engine itself was optimized to the molecule to be as frictionless as possible?
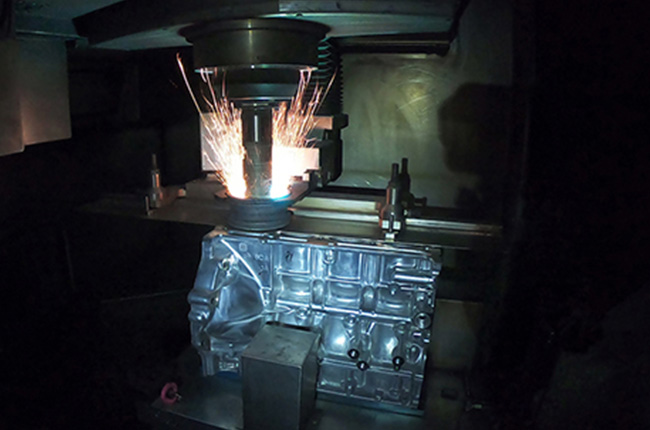
To imagine this, you can take your slippers and slide them across a smooth tiled bathroom floor. It is easy to slip on smooth tiles with slippers, but it is even easier to slip when there is a layer of soap on top of the tiles. Imagine you’re the piston inside the engine, it would be hard to slide on concrete because it would take a lot of speed and force to actually make yourself slide over the surface even with some form of lubrication, but with an already smooth surface, you can glide with no problem.
That’s the analogy we’re using moving forward to describe this technology. In order to extract horsepower and fuel efficiency, friction inside the engine must be as minimal as possible in order to transfer all the kinetic energy to the wheels because friction is the main enemy of efficient movement.
Watch Nissan’s video to see the process happen in real time.
Latest News
-
Hyundai confirms the IONIQ 6 N Launch — Should we expect it in PH? / News
The IONIQ 6 N is coming this July, and Hyundai seems to be leaving its old spoiler behind. With the all-new rear design, the performance sedan could look sleeker than before.
-
Hyundai brings back free roadside help this holy week / News
Hyundai Motor Philippines will once again offer roadside help to travelers during Holy Week. This year marks the third time the program is being done, with select dealers ready to assist on...
-
Ford Philippines is offering a three-year free scheduled service package on their best-selling vehicles this month. / News
Thinking of owning a Ford? Ford Philippines now offers a free three-year Scheduled Service Plan (SSP) on select models.
Popular Articles
-
Cheapest cars under P700,000 in the Philippines
Jerome Tresvalles · Sep 02, 2024
-
First car or next car, the Ford EcoSport is a tough package to beat
Jun 18, 2021
-
Car Maintenance checklist and guide – here’s everything you need to know
Earl Lee · Jan 12, 2021
-
Most fuel efficient family cars in the Philippines
Bryan Aaron Rivera · Nov 27, 2020
-
2021 Geely Okavango — Everything you need to know
Joey Deriquito · Nov 19, 2020
-
Family cars in the Philippines with the biggest trunks
Sep 20, 2023
-
Head to head: Toyota Rush vs. Suzuki XL7
Joey Deriquito · Oct 28, 2020
-
Why oil changes are important for your car
Earl Lee · Nov 10, 2020
-
2021 Kia Stonic — What you need to know about it
Joey Deriquito · Oct 16, 2020
-
Top 7 tips for buying a used car in the Philippines
Joey Deriquito · Nov 26, 2020