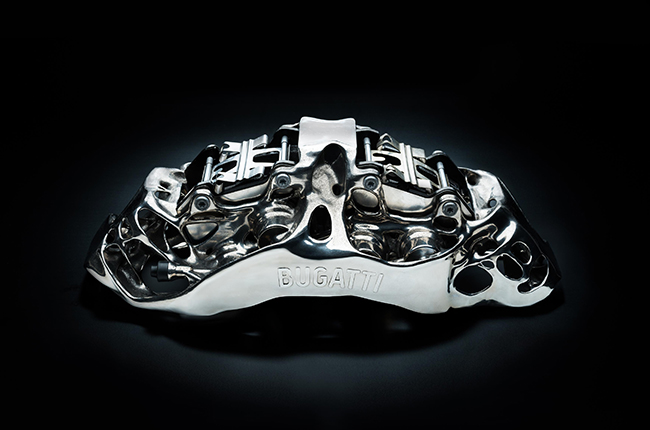
Bugatti is known for its resume of record-breaking hypercars like the Veyron and Chiron. But it seems that the French marque is updating their expertise with something that’s never been done before in the industry - 3D-printing brake calipers.
No, it’s not your ordinary 3D printer that uses plastic goo. This creates an 8-piston monobloc brake caliper made from titanium alloy because super-fast cars need super powerful brakes. In addition, it is the world's largest 3D-printed functional component produced from titanium.
The said titanium alloy used in printing the caliper is the same material utilized in making aircraft components, which makes sense because you’re trying to stop something travelling around 300 kph.
“In our continuing development efforts, we are always considering how new materials and processes can be used to make our current model even better and how future vehicles of our brand could be designed.”
This particular titanium compound has a tensile strength of 1,250 newton per square millimeter which, in layman's term, translates to very high tensile strength. It measures 4,100-mm long, 2,100-mm wide, weighs 2.9 kg, and can be found installed in the Chiron.
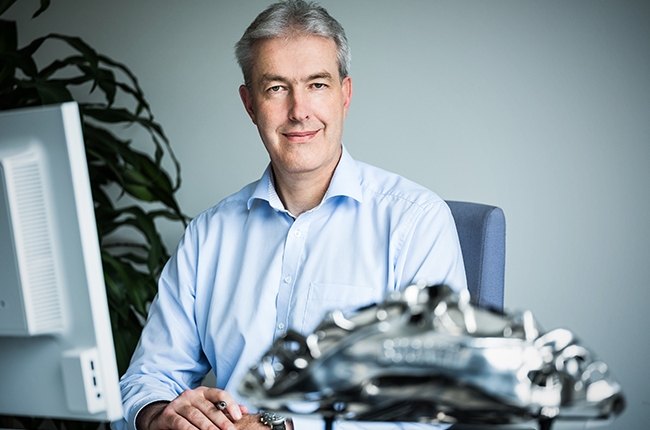
The method was believed to be revolutionary as the normal process of milling titanium to aluminum is almost impossible due to the high strength of the metal. The innovation of 3D printer using titanium opens a wide array of complex structure applications.
The company responsible for fulfilling Bugatti's vision is Laser Zentrum Nord using the largest printer in the world for titanium. This is no ordinary 3D printer as it is equipped with four 400-watt lasers, which is probably not as powerful as the lightsaber from Star Wars but reliable enough to cut through titanium and other metals. All in all, it takes about 56 hours to complete one brake caliper (45 for printing, 11 for contouring).
Latest News
-
Test drive the All-New Elantra at the 2025 Auto Focus Summer Test Drive Festival / News
Hyundai is back on the test drive track, and this time they brought something new. The all-new Elantra is making an appearance at the 2025 Auto Focus Summer Test Drive Festival, and it’s ope...
-
MG kicks off summer test drive event with free treats and more / News
MG is rolling into MOA this week with something for everyone—from gas-powered models to EVs and hybrids. It’s part of the brand’s goal to let more people try their cars firsthand.
-
Toughness and style: Ford unveils special edition versions of the Ranger and Everest Sport / News
Introducing the Ranger and Everest Sport Special Editions, limited edition versions of an already striking duo.
Popular Articles
-
Cheapest cars under P700,000 in the Philippines
Jerome Tresvalles · Sep 02, 2024
-
First car or next car, the Ford EcoSport is a tough package to beat
Jun 18, 2021
-
Car Maintenance checklist and guide – here’s everything you need to know
Earl Lee · Jan 12, 2021
-
Most fuel efficient family cars in the Philippines
Bryan Aaron Rivera · Nov 27, 2020
-
2021 Geely Okavango — Everything you need to know
Joey Deriquito · Nov 19, 2020
-
Family cars in the Philippines with the biggest trunks
Sep 20, 2023
-
Head to head: Toyota Rush vs. Suzuki XL7
Joey Deriquito · Oct 28, 2020
-
Why oil changes are important for your car
Earl Lee · Nov 10, 2020
-
2021 Kia Stonic — What you need to know about it
Joey Deriquito · Oct 16, 2020
-
Top 7 tips for buying a used car in the Philippines
Joey Deriquito · Nov 26, 2020